Temperature control with
Thermoregulators
Temperature controllers help to control the temperatures circulating through water or liquids. Temperature control is ensured by a microprocessor-based thermoregulator that intelligently assists the heating and cooling functions to maintain a constant temperature.
There are 2 variants in the thermoregulators, some can be water and others work with oil, which fulfill the same function of regulating temperatures by means of other cooling equipment such as chillers.
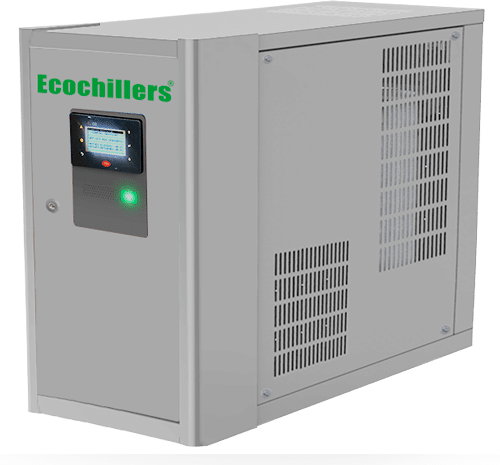
THERMOREGULATORS FOR PROCESSES:
- Plastics industry.
- Medical and/or hospital industry.
- Metal-mechanical industry.
- Information and data industry. Food industry.
- Air conditioning industry.
- Beverage industry. Meat industry and by-products.
- Chemical process industry.

How does a
TCU, Thermoregulator?
A TCU, or Temperature Control Unit, is a system that feeds cooling water, makes changes to its temperature, and directly feeds a specific zone. These thermoregulators offer a series of controls, which allow the user to ensure the set points required by the plant to manage a stable and higher temperature in any equipment that needs chilled water feed such as Mold cavities.
TCUS normally have four pipes. On the one hand, we have the water inlet that comes from the chiller system, and in turn, the outlet that returns the liquid for cooling. Finally we find the pipes that supply the equipment or mold that requires water with specific temperature, and its return, added we eliminate the electrical resistances and take the heat rejection of the compressors we convert it into hot water and thus provide the thermoregulator with water at high temperature if the process requires it.
In addition, the TCU has a recirculation pump, which has the function of increasing the water pressure provided by the TCU, and maintaining constant cooling in the mold. The equipment also has heaters that are submerged at all times, so that if the temperature is too low, the thermoregulator can level it to reach the target temperature.
Venting: When starting up, it is important to ensure that there are no air bubbles inside the equipment, since air is the worst conductor of temperature. The venting has the function of bringing new water from the chiller, expelling the water that could contain bubbles. Venting is stopped when we are sure that there are no bubbles in the system, this is achieved through the automatic air purges that we install throughout the chilled water circuit.

case of success
Plastic Container Injection Plant
At the Bardhal Toluca Plastic Container Injection Plant for its excellent products such as Automotive Oil and Antifreeze, there are numerous pieces of equipment that constantly require cooling in the molds to control their process temperature.
This is achieved by cooling with chillers or coolers, which supply chilled water to the entire operating line. We have a programmed temperature for the plant through the cooling system mentioned above, however, in some parts of the process, we need that temperature to be at a higher point than the rest of the equipment, or even within the equipment itself.
This need is found in injection molding processes. Injection molds need specific temperatures in each of the zones to produce the best quality parts.
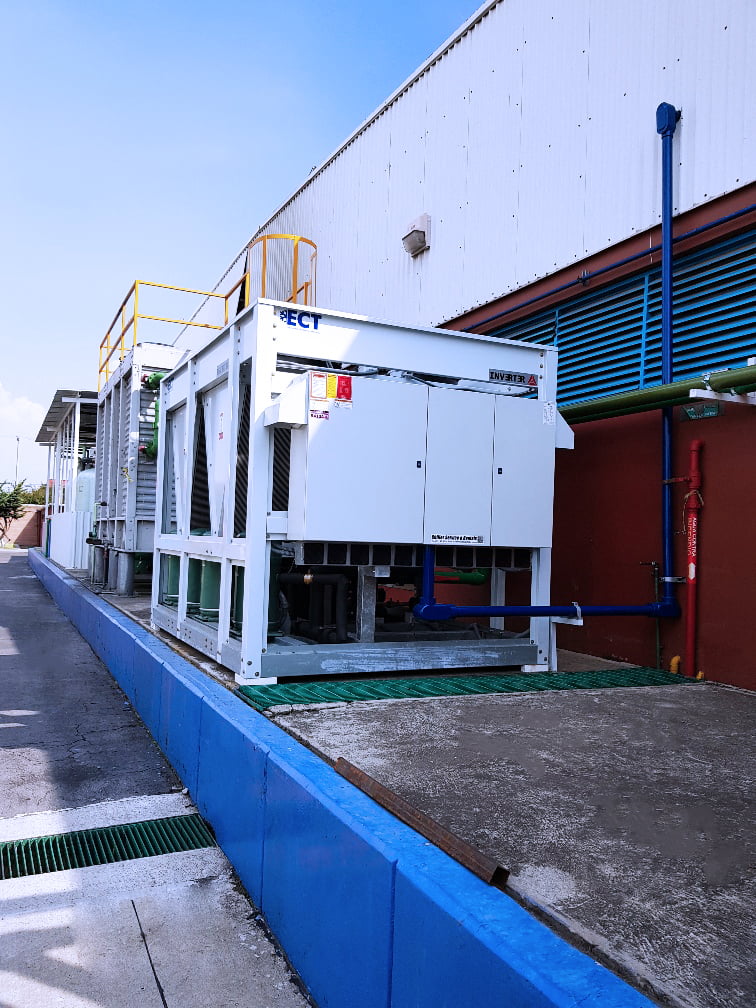
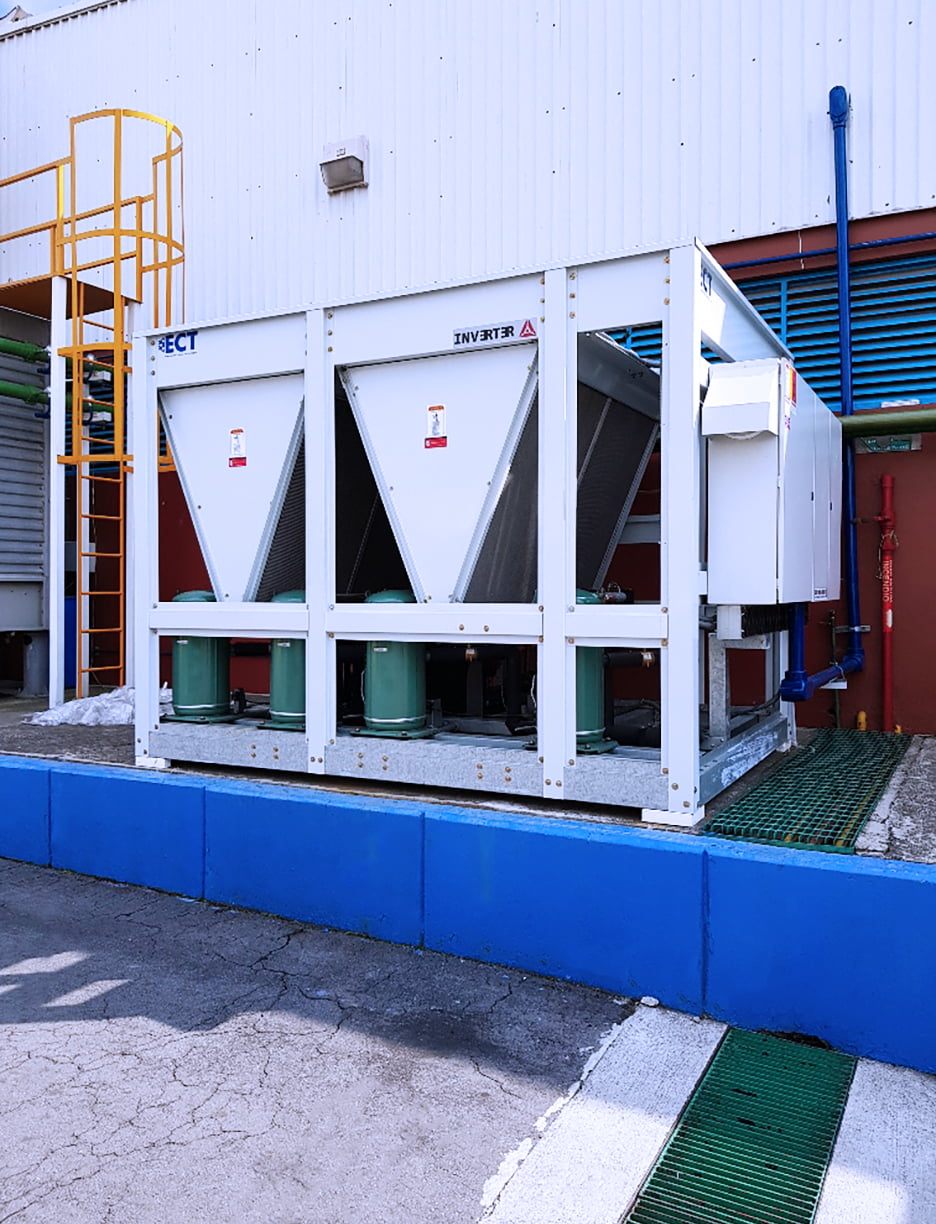
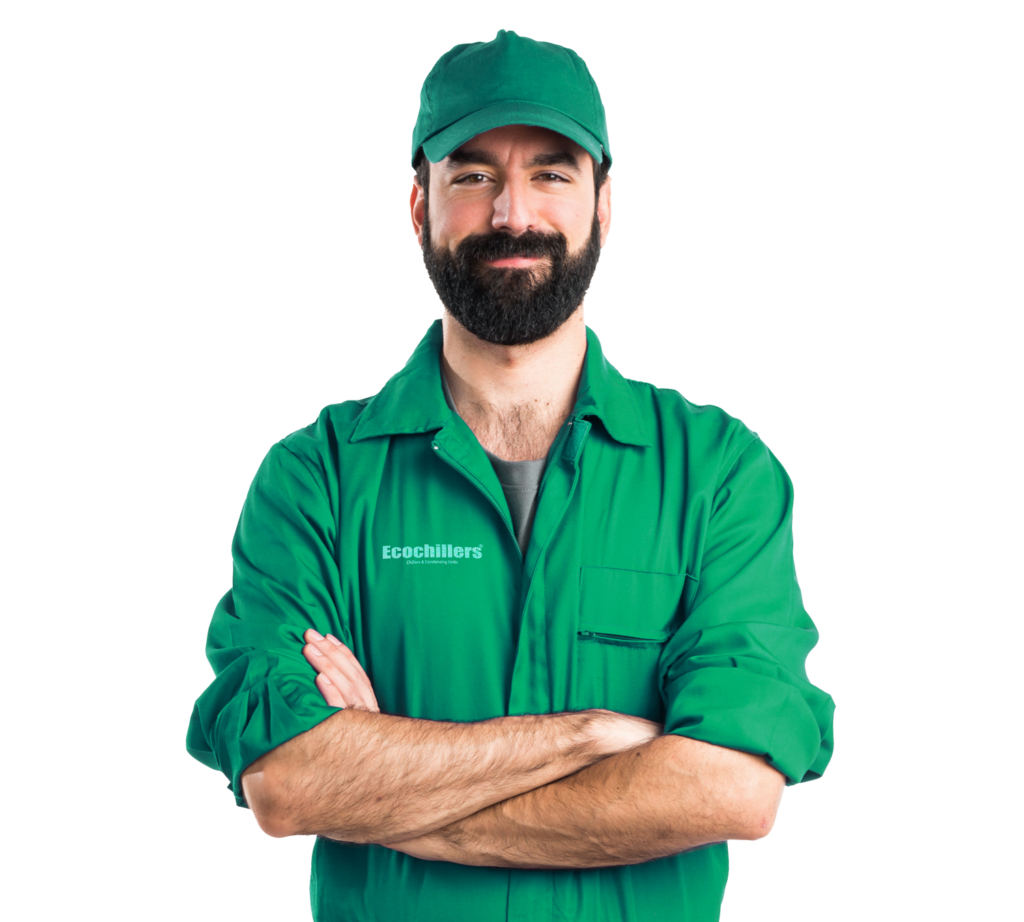